岩沼精工さんを見学しました。金属加工ってなに?工場はどんな感じ?
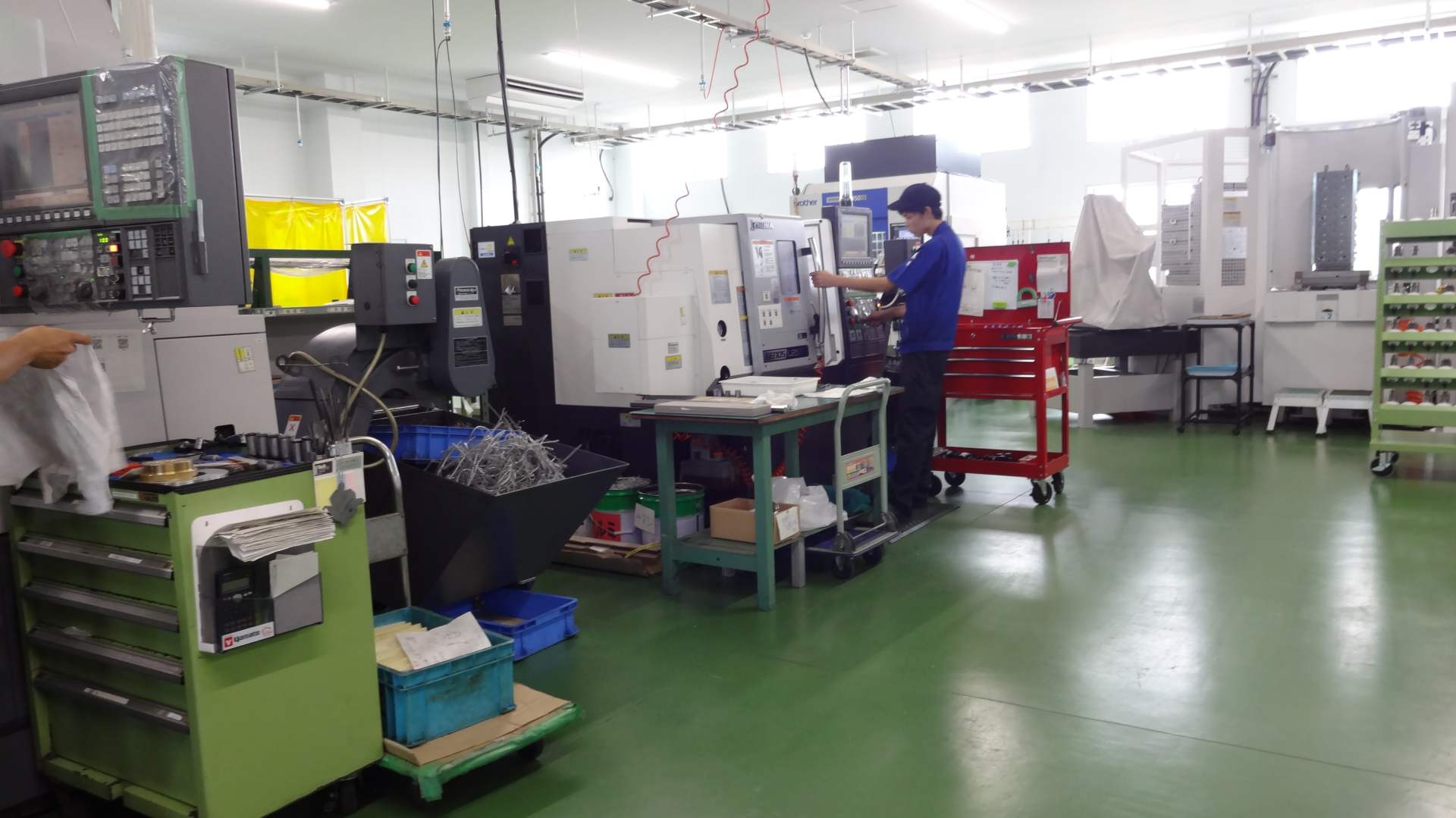
株式会社岩沼精工さんの工場を見学させていただきました。
現在担当しているエフエムたいはくのラジオ番組では、岩沼精工さんほか頑張る仙南の製造業の二代目社長さん達で構成される仙南マシンクラブの皆さんに常日頃から多大なご協力をいただいています。
⇩⇩⇩
仙南マシンクラブの会員さんのご出演記事(未完成)
岩沼精工社長の千葉厚治さんには、
2016.05.26にご出演いただき、
大変興味深いお話を伺いました。
岩沼精工さんと言えば、東日本大震災で大きな被害を受けながら見事に復活した軌跡が有名です。
また、製造業コマ大戦2015で世界3位の成績!を残し、コマ大戦ではその後も好成績を連発して全国版のTVでも紹介されましたし、地方のニュース番組でも何度か放送されました。(岩沼精工 コマ大戦 でぜひ検索を)
ですが、ここでひとつ、私には大きな疑問が。
岩沼精工さんのお仕事は金属加工ということなのですが、金属加工業ってどんな仕事なのか全くイメージがつかめないのです・・・
具体的になにをどうやっているの?
実際はどんな作業なの?
工場はどんな感じなの?
私自身にも3年間の製造業経験がありますが、それはDVD光ピックの組立でした。
ですが、岩沼精工さんは金属加工業なので私が知っている製造現場とはまた別物なのだと思います。
そこで、社長の千葉さんにお願いして岩沼精工さんの工場を見学させてもらうことにしました。
* * * *
index
2016年10月4日。到着!!
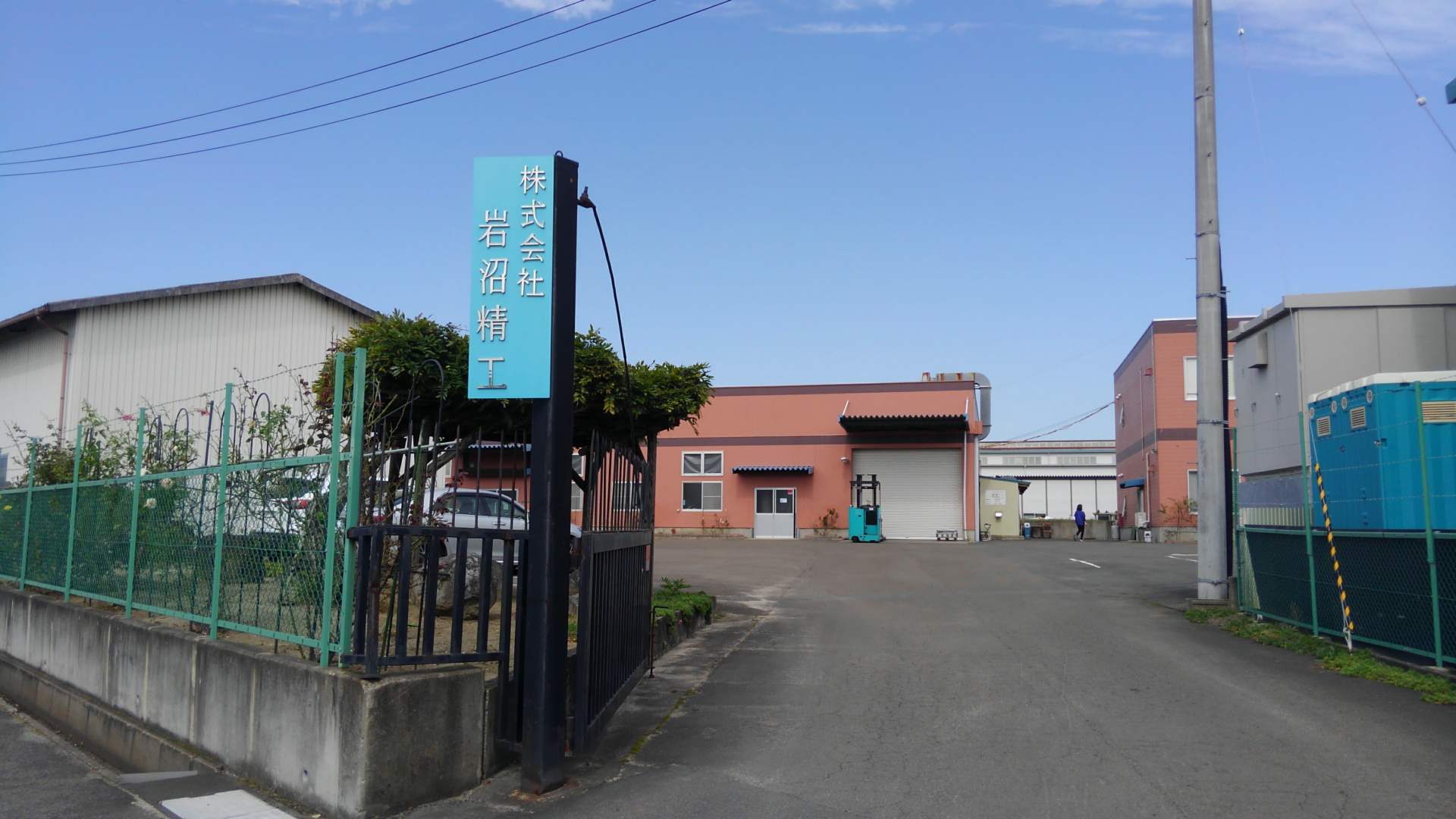
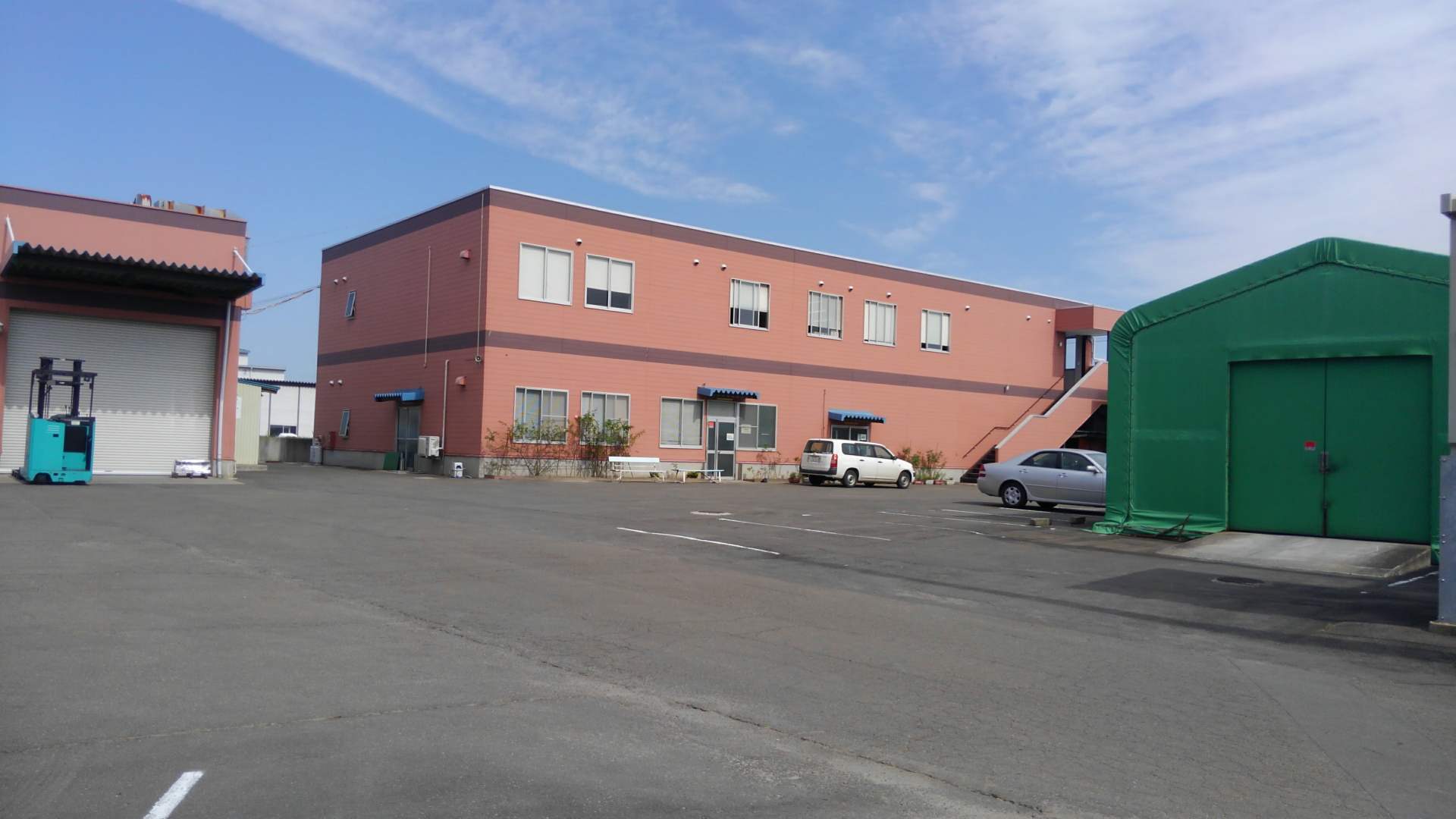
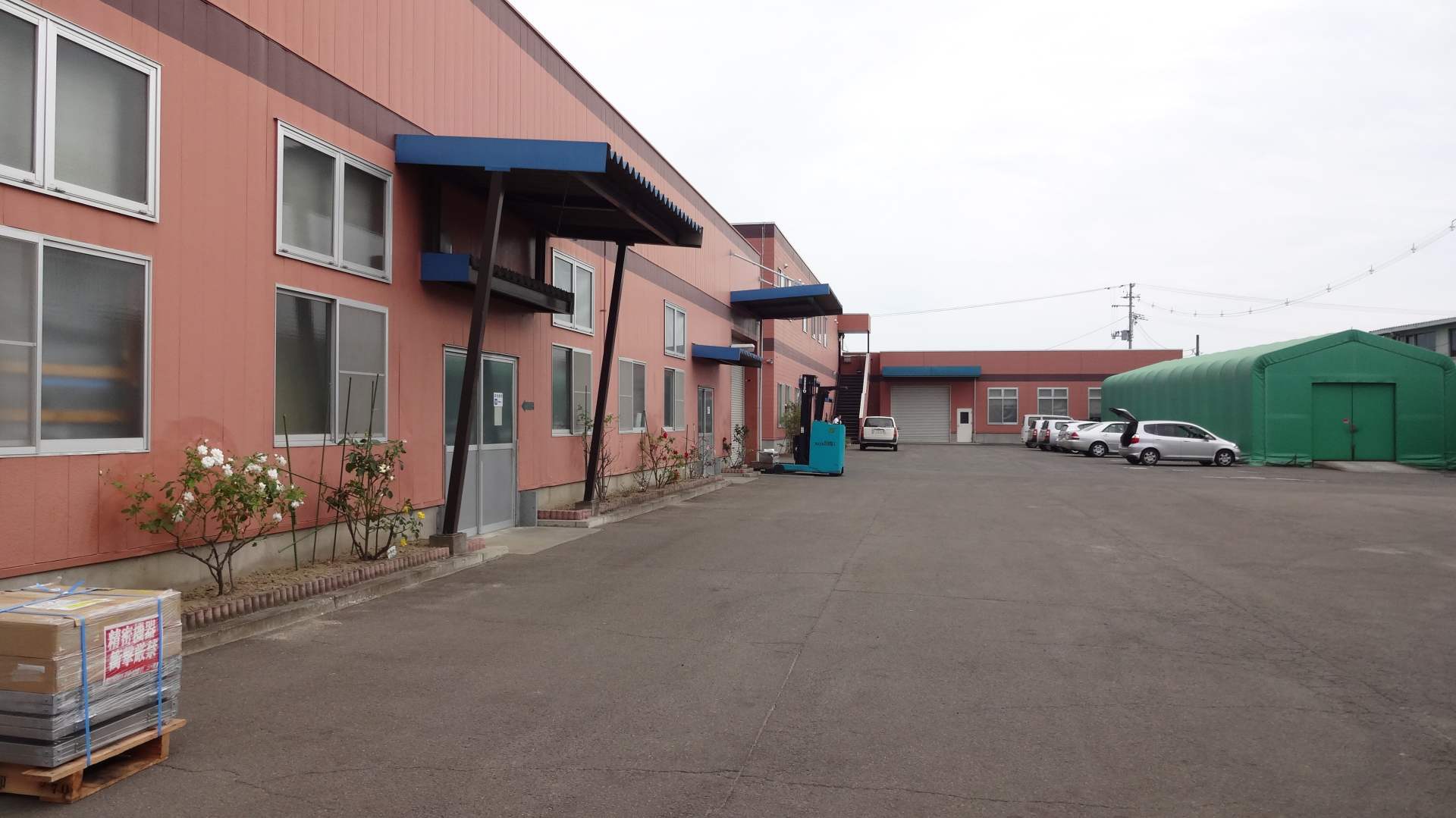
(この続きは現在作成中)
記事を途中でやめてから6年の月日が経ってしまいました・・・
ここから先は6年後の2022年に当時を思い出しながら書いたものです
今日はなんと2022年2月3日です。「到着!」で途切れ「この続きは現在作成中」と書いておきながら、あれから6年も経ってしまいました・・・
中途半端で何もない記事なのに検索で訪れる方がたまにいらっしゃるので、今日の今日まで心苦しく思っていましたが、ここ数日は仕事にも余裕ができたので、当時を思い出しながらようやく(!)続きを書こうと思います。
最初に旧式の工作機械があるエリアを見学
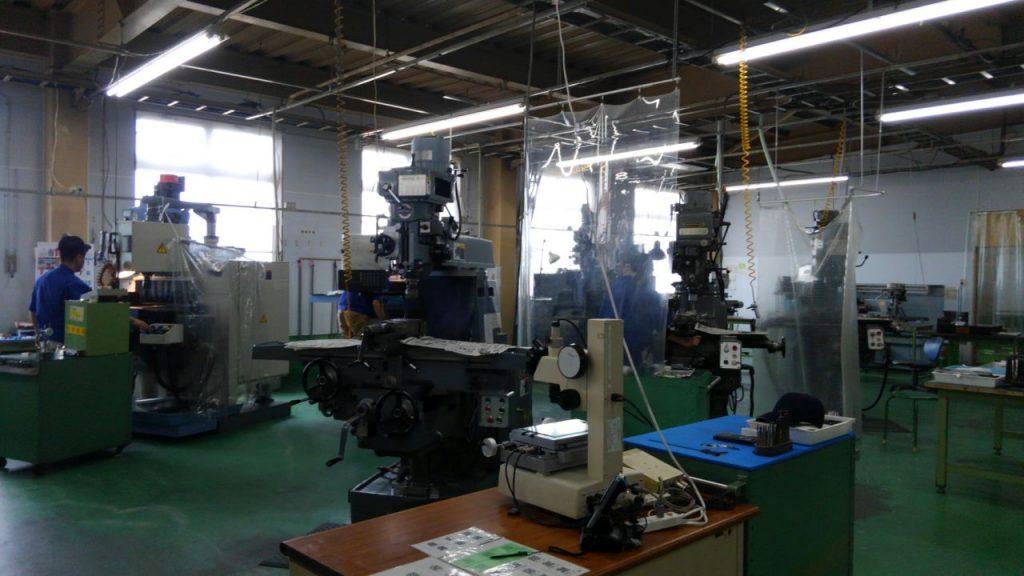
最初に案内していただいたのは旧式の工作機械が並ぶエリアです。
手作業が中心のアナログな装置らしいのですが、新卒で入社した方新人さんたちはここからスタートするそうです。シンプルな機械のほうがしくみが単純で理解しやすく基本が身に付くそうです。
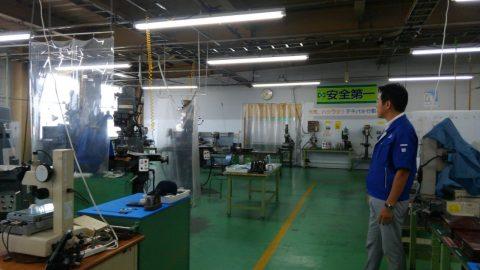
この建物に入ったときに機械の油の匂いがしました。こういう匂いは決して嫌いではありません(むしろ好き)。
それを千葉社長に告げると「え!匂う?匂う?」とすごく気にされている様子だったので、「私はこの匂いが好きですよ」と答えました。
千葉社長によれば工場見学に訪れる高校生にもそう言われた(または言われていないけど社長が気にしている?)ようで、そういったことで応募者に敬遠されるのではないか?と、心配されているみたいでした。
なるほど。製造業は人手不足で求人を出しても応募者が来ないという話は研修先でもよく伺うので、採用の視点から様々なところに気を配っているんだな、と思いました。
シートベルトのバックルを作っていました
↑これはシートベルトのバックルをつくる過程で、今は5~6人かかっている工程を自動化したいと千葉社長が話している動画です。
5年前のこの時点では「ふむふむ」とお話をただ聞いているだけでしたが、今なら何を意味しているかよく理解できます。千葉社長が「このラックもあるし」と言葉にしているラック(動画にも映っている)は、メッキのときに製品をいっぱいぶら下げるラック(治具)ですね。
製品を何十個、何百個とこのラックに引っ掛けた状態でメッキの液に浸すのですが、この引っ掛け作業は人が手でやるんです。
実はこの4年後にケディカ北上工場さんでメッキ加工を見学させていただいていたので、千葉社長のお話がようやく今頃つながった次第です。
つまり金属を加工するだけでなく、加工した製品を機械が並べて機械がラックにかけて機械がメッキの液に浸して引き上げたラックから取り外すところまで自動化したい(!)というお話です。それはすごいわ(←今頃理解・・・)
プレス加工
上の2つはどちらもプレス加工の様子です。(と、今なら書ける)
テープのように薄い金属の帯を機械でジャカジャカ打ち抜いていきます。
これもその後、2019年10月4日に石巻で順送金型を製造しているナカトガワ技研さんを見学させていただいたことで、今はそれほど珍しく感じませんが、このときは薄くて小さな端子がこうやってつくられていることを想像したこともなかったので、とても新鮮で感動しました。
※ナカトガワ技研さんはミカド電装商事さんのブログ記事のために見学させていただたいものです。そのときの記事はこちらです。
マシニングセンターはスポーツセンター?のようなものだと思っていた
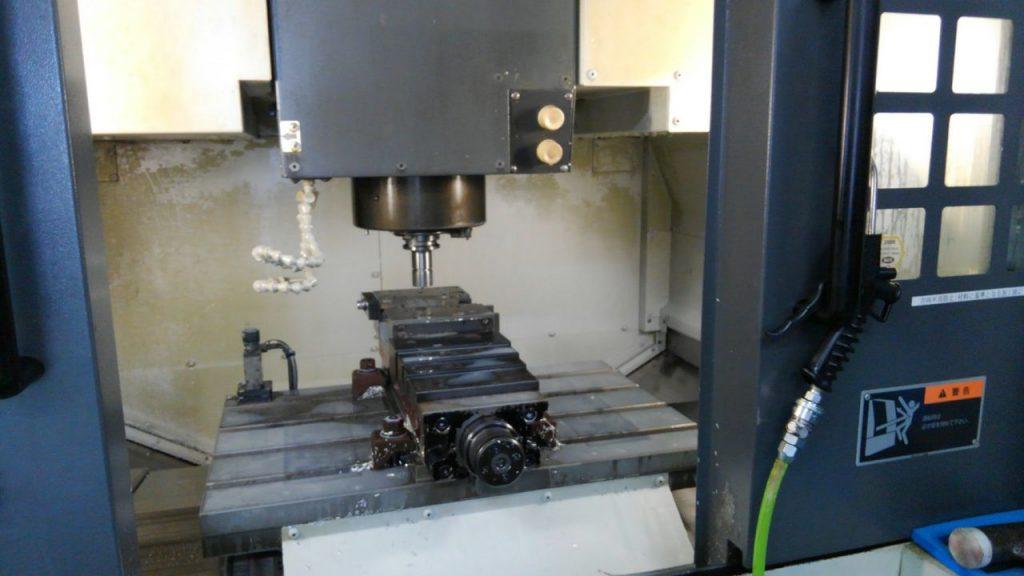
↑こちらはマシニングセンターという装置だそうです。
私が当時担当していたコミュニティFMのラジオ番組で、ゲストの仙南マシンクラブの皆さんがたまに番組の中で「マシニングセンター」という言葉を話していました。
けれどその頃の私は金属加工にまったく不案内だったため、「センター」という単語があるのだから、何かがどこかの場所に集中している(たとえば)スポーツセンターのようなものか?と思っていました^^
「センター」という言葉のイメージがそうだったんです。
ですが千葉社長のお話を伺って今までの(間違った)幻想がガラガラを音を立てて崩れました・・・1台の機械を「センター」と呼ぶなんて、一般人にはとても思いつきませんよー?
こちらで確認したところ「マシニングセンター」とは、"中ぐり、フライス削り、穴あけ、ねじ立て、リーマ仕上げなど多種類の加工を連続で行えるNC工作機械"で、"自動で工具を交換できるATCが特徴"とのこと。
要するに、工具の交換や人手による作業を行うことなく、一度セットすればすべての加工をすべて自動的にやってくれて完成品までをそれ一台でオートメーションで仕上げてくれる工作機械・・・ということでしょうか?つまりセットしてボタンを押せば、次に出てくるのは完成品という機械です。
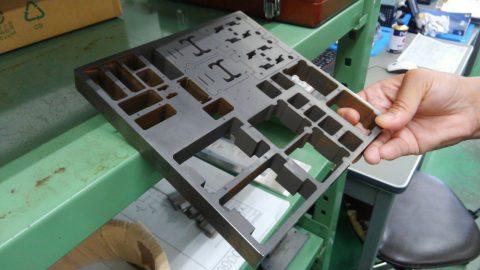
↑マシニングセンターではプレス加工(薄板のくり抜き)とは違って、こういった厚みのある素材からCADデータに基づき立体的に切り出していくことができるそうです。
こういうのを見るのは初めてなので妙に感激してしまいました!
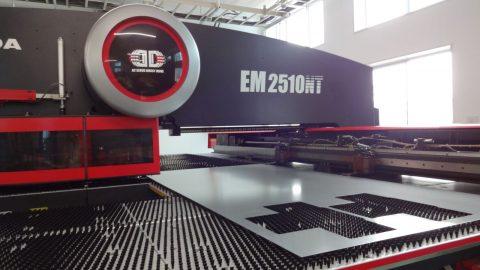
↑こ、、これは何と呼ばれているのでしょうか?AMADA EM 250NT という大きな工作機械がありました。近年導入されたというお話でした。
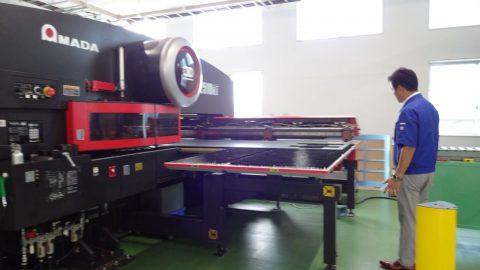
ネットで検索するとこれはタレットパンチ(略称タレパン)という装置で、大きな意味ではプレス加工機の仲間らしいのですが、畳1畳分以上ありそうな厚みのある板を、こちらもCADデータに基づいて高精度でくり抜くことができます。
金属加工は素材も工法も多種多様
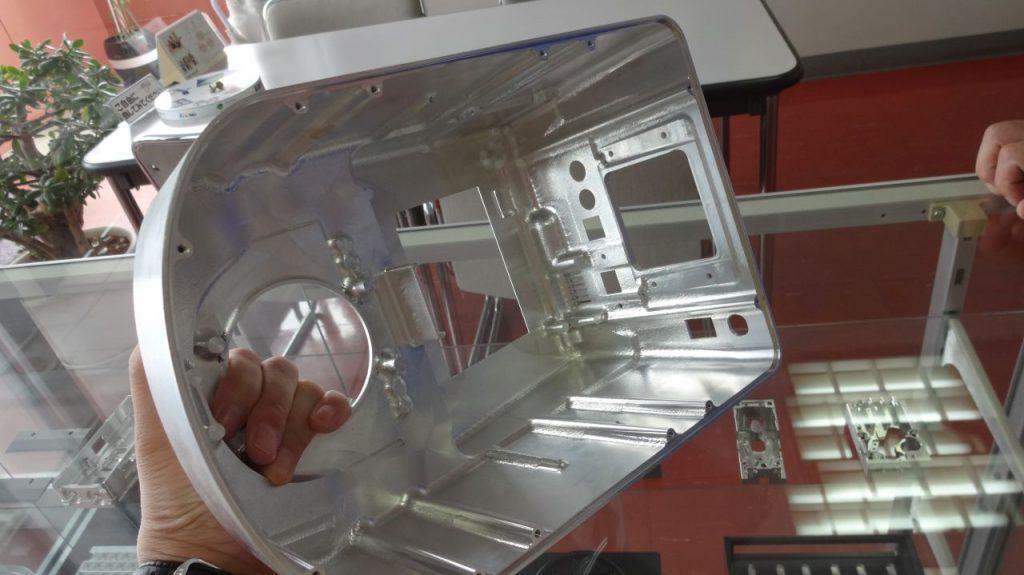
↑上の写真は工場見学を終えてから千葉社長に見せられた加工品です。
「これ、どうやってつくると思いますか?」
何の部品だったかすっかり忘れてしまいましたが、薄い金属の板が立体的に仕上がっているので、私は金属板を上から押して(プレス?)成型するのだと思いました。
すると私の答えは不正解。これも(確か)マシニングセンターで作っているのだそうです。この形が取れる大きな立体ブロックをスパーク(?)で緻密に削っていくとのこと。びっくりです。
自分の記憶では、「こういう一点物はそのほうがずっと安上がり。金型をつくるとそれだけで400万円ぐらいかかる」と言われたような気がします。
試作品なのか、量産品なのかで予算も異なり成型する方法も色々違ってくるんですね。
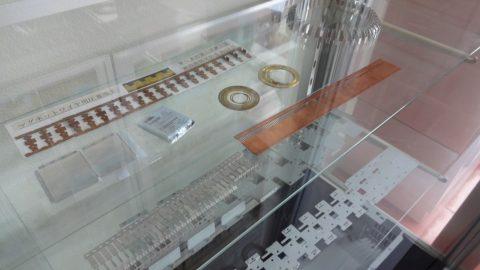
最後にショーケースの写真を撮らせていただき、初めての金属加工工場見学が終わりました。
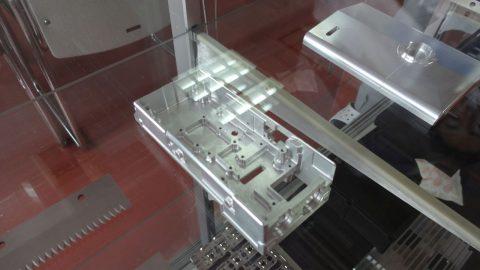
私はその後色々な工場を見学するようになり、5年半後に書き足したこの記事は、今だから書ける内容もあります。
その意味ではまさに岩沼精工さんが工場見学のスタート地点。忙しい時間を縫って案内を解説をしてくれた千葉社長には心から感謝したいです。どうもありがとうございました。